Autonomous Ground Robots for Construction Site Inspection
How Q-UGVs are enhancing safety, efficiency, and real-time visibility across large-scale construction environments.
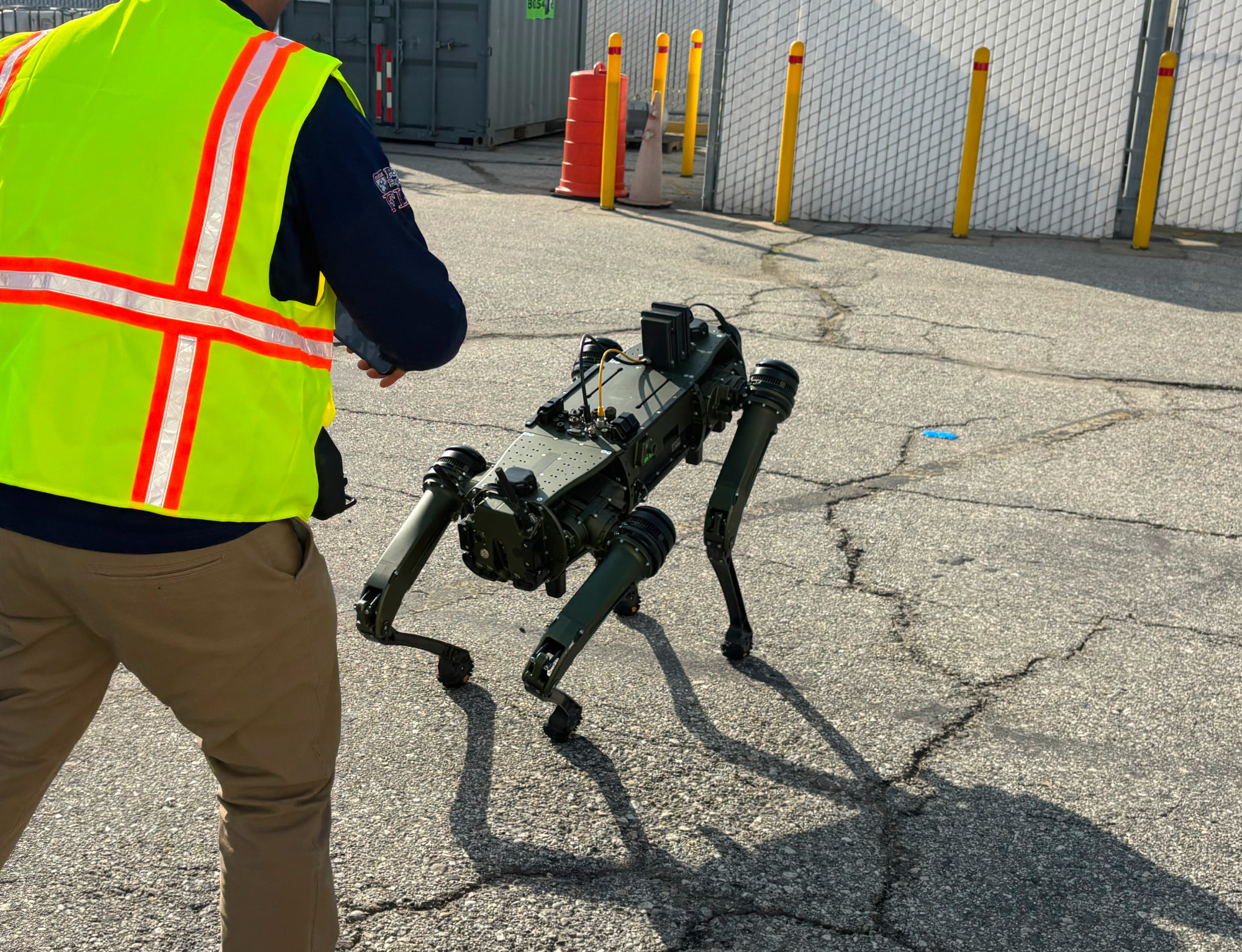
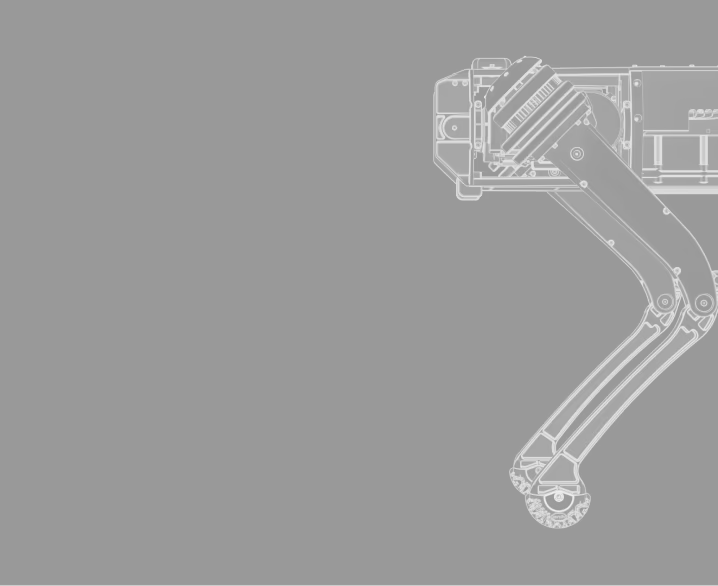
Introduction
The Challenges
Large construction sites present hazardous and constantly changing environments, with uneven terrain, debris, blind spots, and moving machinery.
- Supervisors and inspectors must frequently navigate these areas for safety audits, progress tracking, and equipment monitoring—a process that is time-consuming, dangerous, and labor-intensive.
- Traditional surveillance and inspection tools like fixed cameras or drones fall short in ground-level assessment, particularly inside structures or in low-visibility areas.
Units Deployed Globally
Units Deployed Globally
Solution
Our Approach
Ghost Robotics deployed quadrupedal unmanned ground vehicles (Q-UGVs) equipped with advanced perception payloads—LiDAR, 360° cameras, thermal sensors—for autonomous inspection and site surveillance.
Key tasks included:
- Daily autonomous patrols to monitor safety hazards, structural changes, and materials.
- Real-time data streaming to project management software for progress tracking.
- Hazard detection (e.g., spills, loose cables, heat anomalies).
- Navigating indoors and outdoors across dynamic terrain, including scaffolding and debris zones.
Results
The Results
- Reduced manual inspection time by 40%, freeing up safety officers and engineers for higher-value tasks.
- Increased incident detection accuracy through thermal and visual monitoring, preventing potential safety violations.
- Enhanced site documentation by providing time-stamped 3D maps and imagery of work areas.
- Improved compliance and auditing through automated reporting and historical inspection records.
- Demonstrated resilience in dusty, muddy, and debris-filled environments, operating rain or shine.
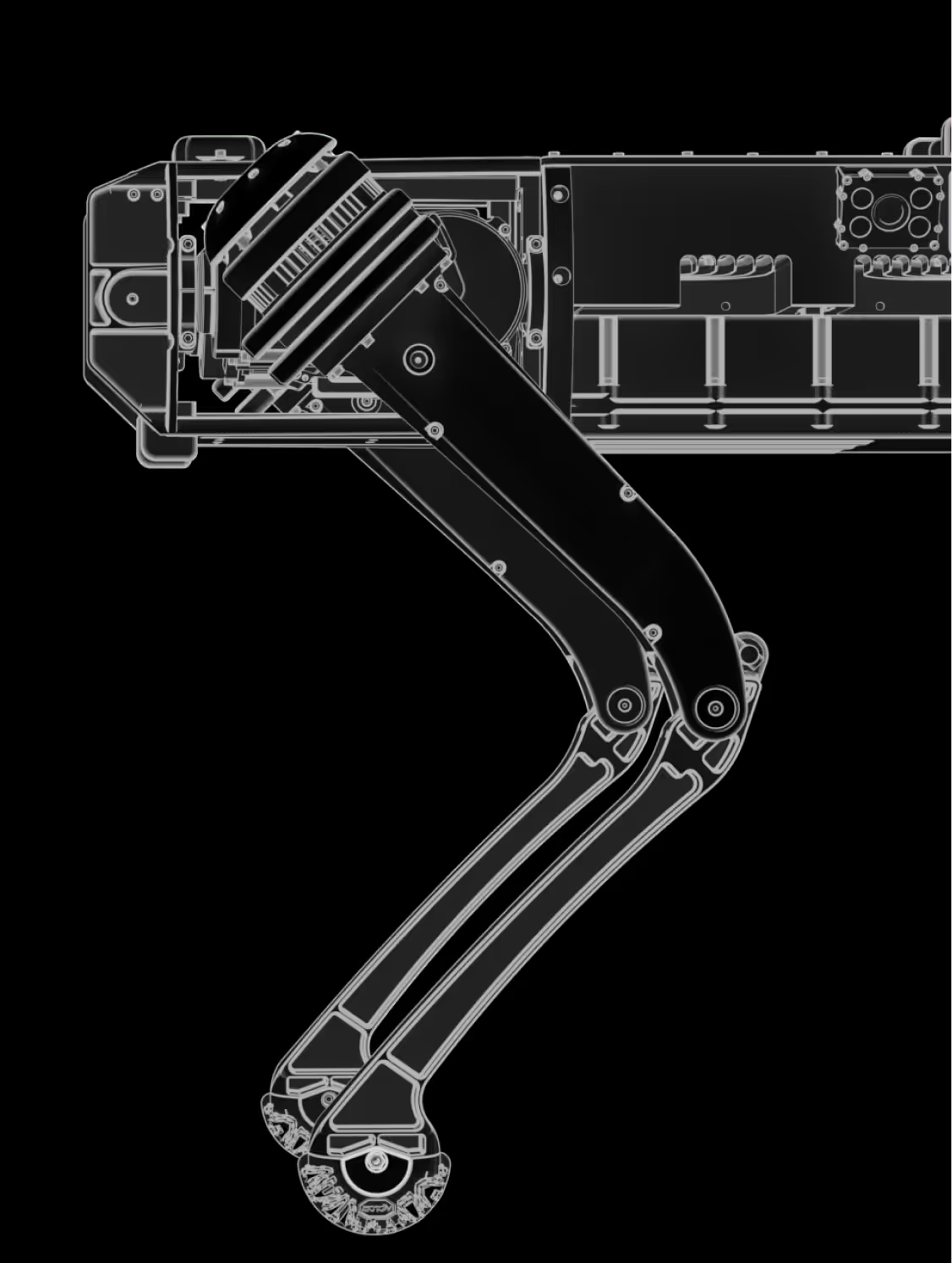